Injection Molding Mold Design Making
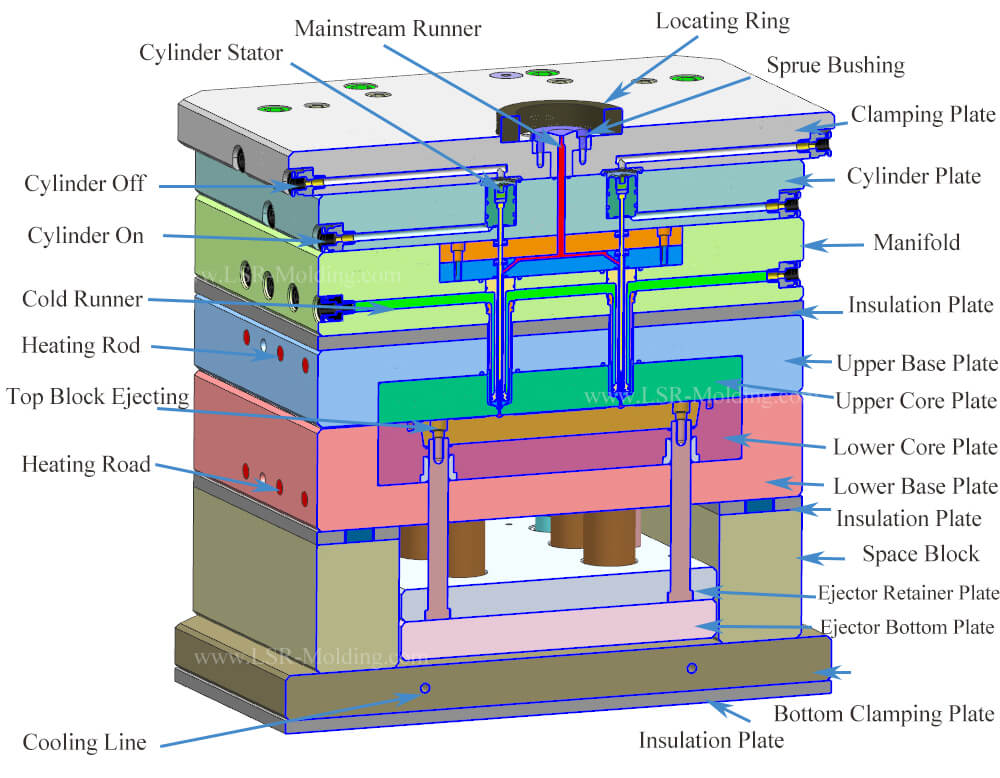
Lsr Mold Design Guide Liquid Silicone Rubber Injection Molding Before you can produce a series of plastic products with injection molding, you need to design and create a proper mold. in this video, you’ll learn the fund. The mold making process involves the following steps: design: the mold is designed using computer aided design (cad) software, which allows for precise measurements and customization. the design process involves creating a 3d model of the part to be molded, which is then used to design the mold.

How A Plastic Injection Mold Works Injection Mold Design Mould Injection molding is a manufacturing technology for the mass production of identical plastic parts with good tolerances. in injection molding, polymer granules are first melted and then injected under pressure into a mold, where the liquid plastic cools and solidifies. the materials used in injection molding are thermoplastic polymers that can. 1. design the mold in cad. first, pick the cad software tool of your preference to design the mold insert. we’ll use the open source blender, but the workflow should be fairly similar in any other cad software. download the blank mold insert design files —you’ll use them to create your injection mold design. 5 steps of the plastic mold injection process. to create high quality parts with consistency and efficiency, manufacturers must follow the following injection molding steps, from mold design to cooling and ejection. step 1: mold design and creation. this initial step is critical as it shapes the entire plastic injection molding process. A portion of the mold that is pushed into place as the mold closes, using a cam actuated slide. typically, side actions are used to resolve an undercut, or sometimes to allow an undrafted outside wall. as the mold opens, the side action pulls away from the part, allowing the part to be ejected. also called a “cam.”.

The Basic Process Of Injection Molding Mold Design Winwinmold 5 steps of the plastic mold injection process. to create high quality parts with consistency and efficiency, manufacturers must follow the following injection molding steps, from mold design to cooling and ejection. step 1: mold design and creation. this initial step is critical as it shapes the entire plastic injection molding process. A portion of the mold that is pushed into place as the mold closes, using a cam actuated slide. typically, side actions are used to resolve an undercut, or sometimes to allow an undrafted outside wall. as the mold opens, the side action pulls away from the part, allowing the part to be ejected. also called a “cam.”. Material selection – injection molding can process a wide range of thermoplastic and thermosetting polymers. a key design aspect is the selection of polymers and additives. mold design – molds are hardened steel and consist of stacked plates, cavity, core etc. they include channels for fill, cooling, vents for air, linear bearings, ejector. 5. gate location. gate location ideally should be specified by a designer, molder and tool maker. gate location is critical to virtually every attribute of an injection molded part. it affects appearance, warpage, tolerances, surface finish, wall thickness, molded in stresses and physical properties, to name a few.

Mold Design Tutorial Moldmaking Resource Material selection – injection molding can process a wide range of thermoplastic and thermosetting polymers. a key design aspect is the selection of polymers and additives. mold design – molds are hardened steel and consist of stacked plates, cavity, core etc. they include channels for fill, cooling, vents for air, linear bearings, ejector. 5. gate location. gate location ideally should be specified by a designer, molder and tool maker. gate location is critical to virtually every attribute of an injection molded part. it affects appearance, warpage, tolerances, surface finish, wall thickness, molded in stresses and physical properties, to name a few.

One Picture To Understand The Structure Of An Injection Mold
Comments are closed.