Plastic Injection Mould Tooling Design Injection Mold Plastic ођ
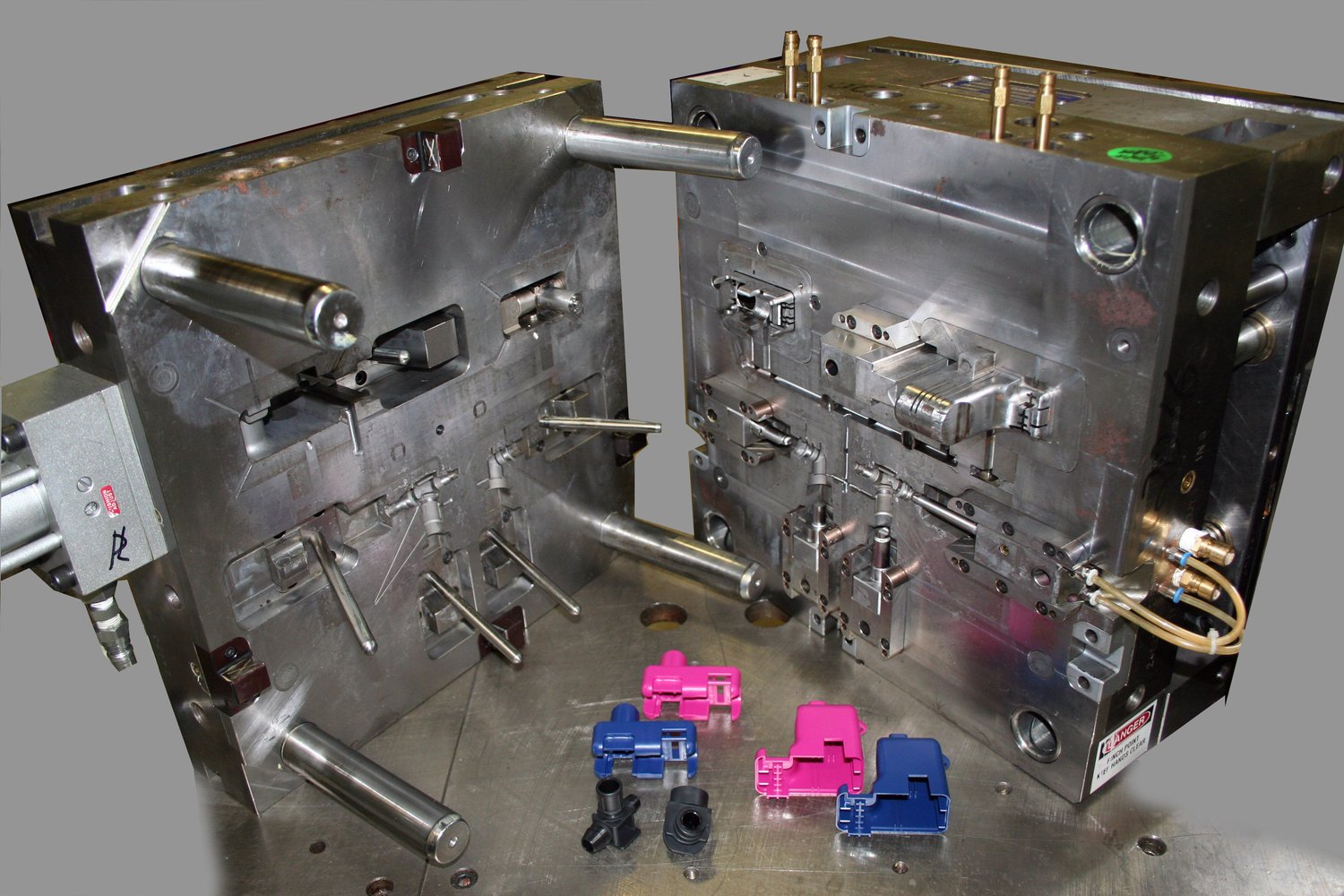
Plastic Injection Mold Tooling Injection Molding Tool Designо The final injection molding tooling solution is customized to meet the client’s project requirements, performance criteria, and budget. every mold is different and costs can vary depending on part complexity, required characteristics, and volume demands. the majority of the cost for plastic injection molding is machining the injection mold. 5 steps of the plastic mold injection process. to create high quality parts with consistency and efficiency, manufacturers must follow the following injection molding steps, from mold design to cooling and ejection. step 1: mold design and creation. this initial step is critical as it shapes the entire plastic injection molding process.

Plastic Mould Tooling Plastic Injection Mould Tooling The two types of gates are as follows: 1. automatically trimmed gates: gates that incorporate features in the tool to break or shear the gate as the molding tool is opened to eject the part 2. manually trimmed gates: gates that require an operator to separate parts from runners during a secondary operation. A plastic injection mold is a sophisticated tool used in the injection molding process to shape molten plastic into specific parts or products. it consists of several components that work together to create the desired part. here are the main components of a plastic injection mold: cavity plate: the cavity plate forms the exterior surface of. These tools, typically crafted from steel, are the workhorses of the injection molding process. molten plastic is injected under high pressure into the mold cavity, taking on the mold's shape and solidifying into the final part. without this crucial tooling, replicating plastic parts consistently and efficiently wouldn't be possible. Melting – the plastic moves into a heated barrel where it melts and mixes uniformly. injection – the molten plastic is then pushed into a closed mold cavity at high pressure, ensuring it is completely filled. cooling – the plastic then cools and solidifies into the desired shape. ejection – the mold opens, and the cooled finished part.
Comments are closed.