The 3 Manufacturing Cost Direct Material Direct Labor And Manufacturing Overhead

Ppt Management Accounting A Business Partner Powerpoint Presentation However, even pricing a product as a loss leader requires analysis of the three categories of costs: direct materials, direct labor, and overhead. direct materials. direct materials are those materials that can be directly traced to the manufacturing of the product. some examples of direct materials for different industries are shown in table 4. Company a is a manufacturer of tables. its product costs may include: direct material: the cost of wood used to create the tables. direct labor: the cost of wages and benefits for the carpenters to create the tables. manufacturing overhead (indirect material): the cost of nails used to hold the tables together.

The 3 Manufacturing Cost Direct Material Direct Labor And Figure \(\pageindex{1}\): work in process inventory. direct materials, direct labor, and manufacturing overhead enter the work in process inventory as the costs associated with the products that are in production. once the products are completed, their costs are transferred to the finished goods inventory. The company purchases $1,000 worth of new materials to make product x. now, the total inventory value is: $1,500 $1,000 = $2,500. after manufacturing product x, let’s say the company’s ending inventory (inventory left over) is $500. this means, the cost of direct materials is: $2,500 – $500 = $2,000. The total cost of manufacturing a product has three elements, namely: raw materials used (or direct materials cost) direct labor (or direct wages) production overhead (or factory overhead or works overhead) a manufacturing business maintains separate raw materials purchase accounts for each type of raw material that its factory uses. Add direct material ($17,000), direct labor ($80,000), and manufacturing overhead ($170,000) to arrive at the total manufacturing cost for the year, which is $205,000. rose burn should take this.
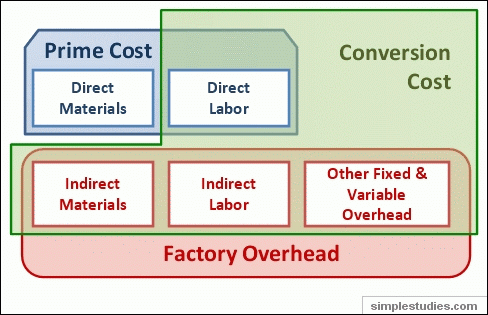
Manufacturing And Non Manufacturing Costs Online Accounting Tutorial The total cost of manufacturing a product has three elements, namely: raw materials used (or direct materials cost) direct labor (or direct wages) production overhead (or factory overhead or works overhead) a manufacturing business maintains separate raw materials purchase accounts for each type of raw material that its factory uses. Add direct material ($17,000), direct labor ($80,000), and manufacturing overhead ($170,000) to arrive at the total manufacturing cost for the year, which is $205,000. rose burn should take this. Manufacturing cost. manufacturing cost is the sum of costs of all resources consumed in the process of making a product. the manufacturing cost is classified into three categories: direct materials cost, direct labor cost and manufacturing overhead. [1] it is a factor in total delivery cost. [2]. Manufacturing overhead (also referred to as factory overhead, factory burden, and manufacturing support costs) refers to indirect factory related costs that are incurred when a product is manufactured. along with costs such as direct material and direct labor, the cost of manufacturing overhead must be assigned to each unit produced so that.
Comments are closed.