Ways To Use Undercuts Successfully In Injection Molding Design
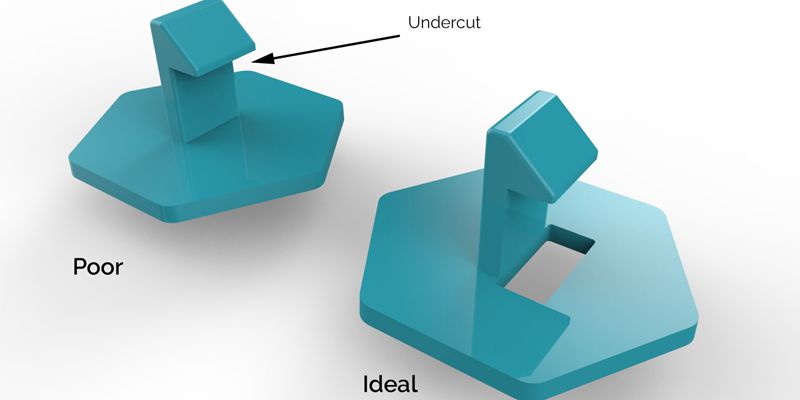
Ways To Use Undercuts Successfully In Injection Molding Design 3. bumpoffs. bumpoffs are an easy way to mold lens covers, container caps, and similar parts with functions that call for them to snap into place. rather than use a side action cam, an insert is machined so the undercut can be applied and is bolted into the mold where a pocket matches the insert dimensions. 1. custom inserts. using the undercut injection molding process, you can create custom inserts that fit into larger parts. machinists often use this insert type in medical devices or products that need an exact fit. you can also use undercut inserts as an alternative to screws or rivets when attaching two pieces. 2.

Ways To Use Undercuts Successfully In Injection Molding Design 1. draft angles: the simplicity of smoother release. draft angles stand as one of the fundamental solutions to address undercuts in injection molding. these are tapered surfaces incorporated into the part design that enables smooth part release without sticking. Draft angles. your parts should have sufficient draft angles to help it be more easily ejected from a mold. a draft angle is a tapered angle that is applied to the vertical walls of an injection molded part. in general, you will want your part to have one degree of draft per one inch (2.2 cm) of cavity depth. Creating undercuts in injection molding requires specialized techniques. let's explore the most common methods and their pros and cons. 1. parting line adjustment. parting line placement is crucial for undercut design. it involves: aligning the parting line with the undercut feature. splitting the undercut into two halves. Here are 5 ways that can help you effectively deal with undercut molding designs. 1. position parting lines. the parting line is the intersection plane between both molds. by positioning the parting line right on the protruding feature, you can avoid the undercutting problem.
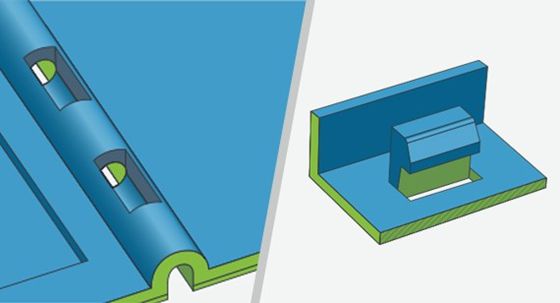
Ways To Use Undercuts Successfully In Injection Molding Design Creating undercuts in injection molding requires specialized techniques. let's explore the most common methods and their pros and cons. 1. parting line adjustment. parting line placement is crucial for undercut design. it involves: aligning the parting line with the undercut feature. splitting the undercut into two halves. Here are 5 ways that can help you effectively deal with undercut molding designs. 1. position parting lines. the parting line is the intersection plane between both molds. by positioning the parting line right on the protruding feature, you can avoid the undercutting problem. A. draft angles: one of the simplest ways to address undercuts is by incorporating draft angles in the part design. draft angles are tapered surfaces on the mold that allow the part to release smoothly without sticking. by adding draft angles, the part is more easily ejected from the mold during the demolding process. Common challenges of injection molding undercuts and their solutions: injection molding undercuts pose several problems, although their solutions can be implemented as described above. mold design complexity: undercuts greatly influence mold complexity. they need extra moving parts, such as side actions or collapsible cores.
Comments are closed.